Nano Diamond Dies: Advances in Wire and Cable Manufacturing
- szwirediecom24
- Apr 22, 2023
- 3 min read
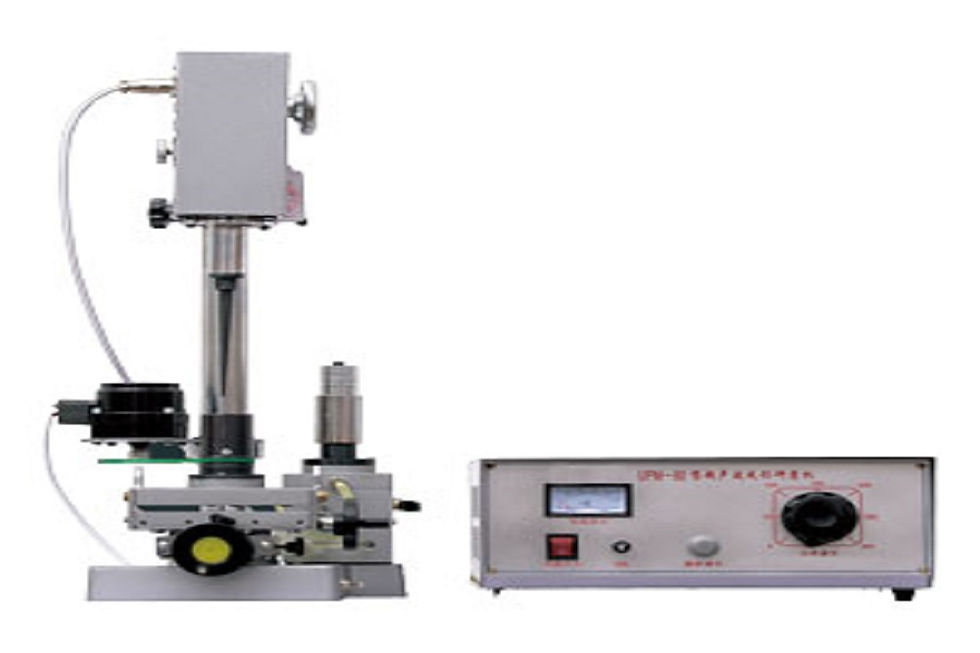
With the advancement of new technologies and materials, the wire and cable industry is constantly evolving to improve efficiency and performance. In recent years, nano diamond dies have been used in wire and cable manufacturing for the first time. In addition to improving wear resistance, increased hardness, and enhanced thermal conductivity, nano diamond dies offer a number of advantages over traditional wire and cable dies.
Wire and cable manufacturing relies heavily on bunching dies, stranding dies, and tube drawing dies. These dies are used to shape and refine wires and cables during the manufacturing process. In contrast, traditional dies are prone to wear and damage over time, leading to reduced productivity and higher costs. On the other hand, nano diamond dies offer significant benefits that can help address these problems.
In addition to their exceptional wear resistance, nano diamond dies have several other advantages. Because the diamond coating on these dies is extremely hard, they can withstand intense pressure and friction during the wire and cable production process without getting damaged. As a result, die life is extended and maintenance and replacement downtime is reduced, improving efficiency and lowering costs.
Furthermore, nano diamond dies manufacturers also offer enhanced thermal conductivity in addition to wear resistance. By doing so, the wire and cable manufacturing process is able to dissipate heat more effectively, reducing the risk of overheating and cable damage. For high-speed production lines, where overheating can be an issue, this is especially important.
As a result of nano diamond dies, wire and cable products are also more consistent and precise. Diamond coating on these dies allows for a greater degree of control over the shaping and refining process, resulting in wire and cable that is more uniform in shape and size. The final product can be more reliable and perform better.
Overall, the use of nano diamond dies in wire and cable manufacturing offers numerous benefits that can help to improve efficiency, reduce costs, and enhance product quality. These cutting-edge tools can be used for bunching dies, stranding dies, and tube drawing dies. Investing in nano diamond dies can help wire and cable manufacturers stay on top of the industry's evolving requirements and continue to produce high-quality products.
Specifically, nano diamond dies are made by applying a thin layer of diamond particles to the surface of a traditional die. This coating is only a few microns thick, but extremely hard and durable. Additionally, diamond particles are extremely smooth, which makes shaping and refining wires and cables easier.
In bunching dies, multiple wires or strands are bundled together to form one, thicker wire, while in stranding dies, multiple wires or strands are twisted together to produce a more durable, strong cable. In the fields of medical devices and automotive components, tube drawing dies are used to shape and refine hollow metal tubes.
In all of these applications, the use of nano diamond dies can offer significant benefits. The enhanced wear resistance of nano diamond dies, for example, can help reduce the frequency of die replacements in bunching and stranding dies, improving efficiency and lowering costs. As a result of the improved precision of these dies, wires and cables can also be more consistent and uniform, improving their performance and reliability.
It is possible to improve the surface finish of the drawn tubes by using nano diamond coatings in tube drawing dies, resulting in smoother, more uniform tubes. In medical applications, the surface finish of the tube can have a significant impact on its biocompatibility and overall performance. Get more info about diamond wire drawing dies.

In spite of being relatively new in the wire and cable industry, nano diamond dies are quickly gaining popularity because of their numerous benefits. By investing in these cutting-edge tools, manufacturers can improve efficiency, reduce costs, and produce better wire and cable products, giving them a competitive advantage.
Using nano diamond dies in wire and cable manufacturing is a significant development that has the potential to transform the industry in the future. These cutting-edge tools offer enhanced wear resistance, increased precision, and other advantages for bunching dies, stranding dies, and tube drawing dies. In the coming years, nano diamond dies will likely become even more widely used in the wire and cable industry, allowing manufacturers to stay ahead of the curve and meet customer demands.
Comments